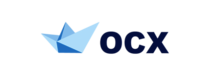
The OCX 2024 AGM was a great success
Posted on at By DNV
What an incredible three days we've just had in Ancona! The OCX 2024 AGM, wrapped up with a memorable visit to the Italian Navy's first Multipurpose Offshore Patrol Ship, the “Paolo Thaon di Revel.”
A huge thank you to the Marina Militare for their gracious hospitality and for allowing us on board their latest vessel “Paolo Thaon di Revel” !
We were thrilled to welcome over 30 OCX members and many non-members, all eager to share insights on the latest OCX developments and engage with fascinating use cases. And of course, we couldn’t have done it without Simon Conti and CNT Technologies, who ensured we enjoyed exceptional Italian hospitality and delicious cuisine!
Participating companies: AITAC, ATENA Ravenna - Emilia Romagna, Bureau Veritas, Cadmatic, Cantiere delle Marche Srl', Chantiers de l'Atlantique, ClassNK, CNT Technologies Srls, Cori Design, DNV, FINCANTIERI SpA, IIS Laeng Meucci, Italia Yachts, Lloyds Register, Lloyd's Register EMEA Trieste Support Office, Marina Militare Italiana, Meyer Turku, NAOS Ship & Boat Design, NAPA, NDAR, NMC ITALIA SRL, NTNU (Norway), Rapid Structural Design Oy, RINA, Royal Van Lent Shipyard, Siemens Digital Industries Software, Studio Tecnico Navale Pattacini, Turk Loydu, ULSTEIN DESIGN & SOLUTIONS AS, Venture Ship Management Europe S.r.l.
A summary from the OCX 2024 AGM event open to all participants
Keynote: Succeeding with 3D and model-based projects - learnings from the construction industry
The keynote presented by Pål Njølstad, COO of Novorender kicked off the fully open part of the OCX 2024 AGM. Novorender highlighted the benefits of moving from drawing-based to model-based projects in the architecture, engineering and construction (AEC) industry. Model-based projects can potentially reduce project overruns from 20% to 5% for this industry. The main cost-reducing factors are fewer mistakes and re-work because all project data is accessible from one single model with linked project data and documentation. The main drivers behind this change are:
- The Building Information Model (BIM) and ISO standards with good tooling support
- A large BIM uptake (particularly in Nordic countries) driven by contracted BIM requirements, mainly for large infrastructure projects and government projects.
The silver bullet question for shipbuilding is whether wether the drivers we see in the AEC industry are transferrable to the shipbuilding industry. This is interestingly discussed in the keynote on the second day presented by Janica Bronson from NTNU. There is no doubt that there is a potential for the shipbuilding industry to benefit from model-based and data-driven projects. The question is if the necessary enablers are in place. One big difference from the AEC industry is how the shipbuilding contracts are set up between the owner and the shipyard where there are still no requirements set out for data-driven and model-based projects.
The OCX standard and the work by the OCX Consortium
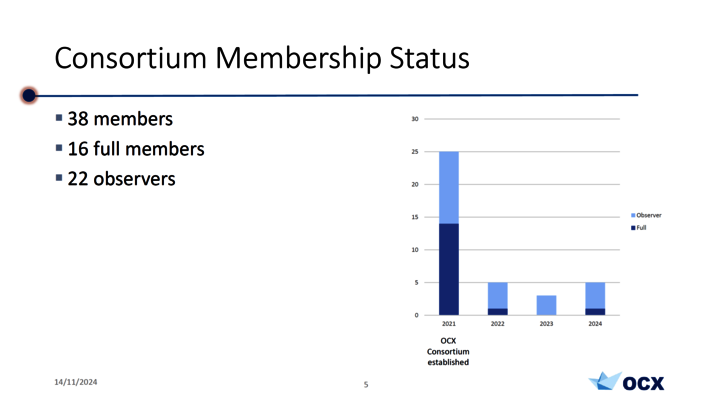
The OCX Chair Ole Christian Astrup presented the state of affairs of the OCX consortium. The number of members has grown to an impressive 38 companies from the shipbuilding industry, representing CAD vendors, PLM integrators, designers/yards, and classification societies. The consortium is still growing, and we hope to have the first owner or manufacturer join soon, as representatives from both attended the OCX 2024 AGM.
The OCX Chair showcased a podcast explaining what the OCX is all about. The podcast was created using the Google notebooklm.google.com artificial intelligence service and a whitepaper on the OCX as input. Spend 6 minutes of your time to listen to the result which is quite impressive.
The consortium now has a fully operative Interoperability Forum. The purpose of the OCX_IF is to accelerate the delivery of production level, use-case tested functionality and cross-platform OCX-based workflows to the market by testing OCX 3D model exchanges between OCX implementors. The OCX-IF recently completed the first test round and will soon publish the full test report.
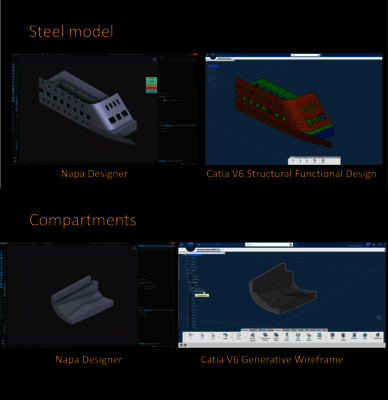
Presentation: The transfer of the vessel arrangement from NAPA Designer to Catia
Sami Gusani, Development Engineer, Meyer Turku presented how Meyer Turku sees how 3D design and the OCX standard can help them build cruise vessels for the future. Meyer Turku is investing in developing carbon-neutral vessels for the future through the Finnish NEcOLEP research project. Throgh this project Meyer Turku plans to investigate the benefits of the OCX standard throughout the whole design process in cooperation with Aalto University, Rapid Structural Design, DNV, NAPA and AITAC. Meyer Turku sees the OCX open format as a catalyst for industry change by
- enabling seamless model exchange between stakeholders and SW systems
- supporting sustainable shipping
- driving digitalisation
- promoting cross-platform collaboration, and
- enabling intelligent technologies across the ship's life cycle
Meyer Turku's ambition is to be a pioneer in transforming shipbuilding and see the OCX as one of the enablers.
Presentation: BV 3D Classification Project
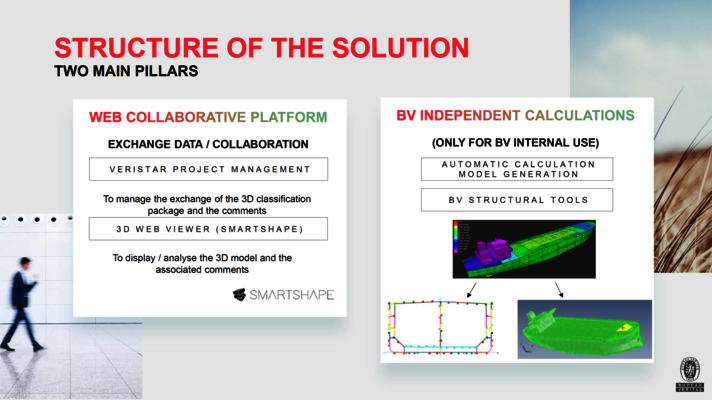
Oliver Degrand, Business OwnerDirector–TechnicalDigital Solutions, Bureau Veritas, presented the approach BV has taken on 3D classification and fully integrating the OCX standard into their processies. The objective of the 3D classification process in BV is to carry out Design approval based on the 3D digital mock-up provided by the designer thereby
- Reduce shipyard workload using the numerical model to avoid generating 2D drawings / Fully digital work process
- Numerical model can be used directly to generate calculation databases and improve quality
- No more inconsistency due to different revisions of drawings to improve quality
- Enhance collaboration and improve customer experience
- Speed up the process of design verification
The BV approach has two main pillars:
- A web-based collaborative platform, Veristar Project Management with the integrated 3D viewer SMARTSHAPE
- BV independent calculations with automated calculation model generation for BV Mars and BV Veristar
The collaboration platform allows all actors (including shipbuilders and owners) to review, edit and exchange information in real-time.
Presentation: 3D Model-based Approval in Reality (JDP VARD/NAPA/DNV)
Myeong-Jo Son, Senior Software Developer Design Solutions, NAPA, and Sverre Bergli, Head of Department, Ship Structures & Stability, DNV presented the joint development project carried out with VARD. Unfortunately, the third author Florin-Ciprian Luli, Senior Engineer Structural Department Vard Design & Engineering, could not attend in person. VARD, NAPA and DNV presented the benefits to VARD and DNV from a fully digital model-based data exchange enabled by NAPA Steel and the DNV 3D Approval Platform. VARD showed how they can reduce the lead time for a model-based project by shifting work from creating 2D drawings into the development of the 3D design model in NAPA steel. By avoiding the creation of 2D drawings and sharing the 3DOCX model with DNV early in the project further lead time can be reduced because the certification approval can be done in parallel with the design development. The potential lead time for a typical project can be up to 6-7 weeks which is a huge benefit in a competitive shipbuilding environment. VARD utilised the DNV 3D approval capabilities to engage with DNV and receive comments and 3D markup of the 3D model.
Keynote: Data Models in Ship Design and Construction - Insights from 4D BIM
Janica Bronson, Ph.D. student at NTNU, kicked off Day 2 of the OCX AGM by presenting the keynote with the subtitle “Insights from 4D BIM and the SEUS Project” together with Professor Henrique Gaspar, NTNU. The keynote summarised the evolution of the Design and Planning data models in the shipbuilding industry with references to several standardisation attempts. Despite a huge effort over the past decades, there is still a lack of a cohesive understanding of a vessel across its entire lifecycle. The main reasons are:
- Formalised Data Model: A lack of formalised data models addressing multi-domain ship data incorporating time, process, and functional information
- Open Standards: A lack of industry-wide data exchange standards impeding interoperability
- Development Workflow: An integrated Product Development Environment (IPDE) which impedes collaboration
- Adoption and tooling: The lack of data management protocols to support the IPDE, modelling standards, and exchange standards
Bronson pointed out that the AEC industry and the Building Information Model is a collaborative process enabled by technology and may possess the capabilities in the form of a Formalised Data Model and a Development Workflow. The OCX has a role as part of a formalised data model covering the data information required by the classification societies but can also solve a part of the shipbuilding interoperability challenge as an open standard, see the figure below.
Presentation: OCX application in an integrated model
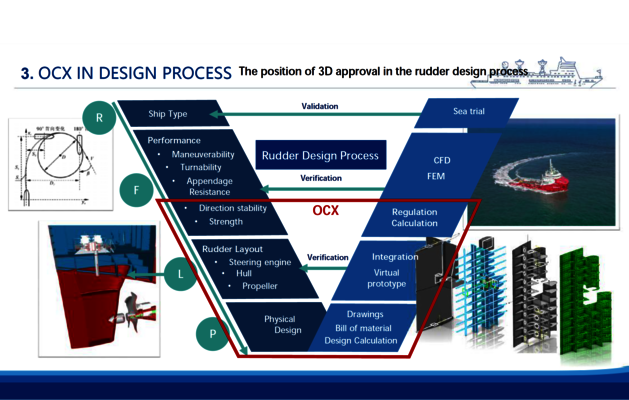
Haiying Zhang, vice director of the IT department of the MARINE DESIGN & RESEARCH INSTITUTE OF CHINA (MARIC), presented how MARIC is approaching model-based design. MARIC's vision is to have a single source of truth based on the 3D mockup through all design stages from concept to approval. this will enable MARIC to
- respond to customer needs
- express design intent
- reduce cost and improve communication and faster closing of class comments
- early identification of risks
- reduce drawings and workload in the detailing phase
MARIC presented an interesting take on 3D component approval by defining a tailormade extension of the OCX schema for the rudder in cooperation with DNV. This allowed MARIC to transfer the 3D rudder 3D model from Dassault 3D Experience to the custom-made OCX schema and DNV to approve the rudder using the 3D model.
Presentation: Ulstein and Cadmatic
Ulstein Design & Solutions presentation
Børulf Lefdal, Senior Principal Engineer, Department Manager, Hull Structure & Outfitting, Ulstein Design & Solutions presented how Ulstein uses Cadmatic and the OCX in their design process. Lefdal showed how Cadmatic can export the 3D model to the 3Docx format and successfully import the 3D model into the DNV calculation tool Nauticus Hull. This allows for the efficient check of the design scantlings, optimisation and ensuring rule conformance. All main scantling information were transferred without any errors. The next step for Ulstein is to use the DNV 3D Aprroval Platform to pilot the full 3D approval process with DNV for a selected design. The expectations from Ulstain to the use of OCX are:
- Shorter time to do scantling of the vessels
- Shorter approval time by Class
- Better quality of the approval by Class
- Less class comments
- Shorter lead time to production
Lefdal pointed out that there are still challenges to be solved regarding the workflow with class, shipowners and flag requirements to drawings, how to process additional loads information in the model, and change management only to mention some.
Cadmatic presentation
Ludmila Seppälä, Business Development Director, presented how Cadmatic is supporting the OCX. Cadmatic sees the OCX as the one interface to all classification societies in the future with expectations to
- Enhance interoperability
- Serve as a universal interface to FE
- and facilitate the approval process with the classification society
Seppäla explained how Cadmatic sees the information management for the Engineering, Approval, Revisioning and stamping process, see the slide below. Interestingly, Cadmatic identifies potential synergies with the BIM Collaboration Format for redlining which can be worthwhile to explore. However, there is no doubt that the OCX fulfils most of the requirements for describing the vessel asset for the steel structure.
View the full Ulstein presentation View the full Cadmatic presentation
Presentation: OCX in Action: Simplify your FE-analysis workflow
Michel Pudd, Customer Relations Manager, Rapid Structural Design presented how RSD and FEMap can speed up the FE-analysis workflow using OCX. The traditional FE analysis process is slow, not delivered on time, costly, does not match 100% with the design, inconsistent and inflexible. All these problems are rooted in only two factors:
- Frequent changes and design updates
- Contradicting source information
RSD sees the OCX as a Rubik's cube that can solve this puzzle. The OCX contains all the information to automate the FE modelling and meshing for both global and local models. A traditional FE-analysis manual modelling effort takes 40 hours for a global cruise model. This time can reduced to 8 hours by utilising the OCX model. More importantly, this allows RSD to carry out the FE analysis at a later stage in the design process when the design is more mature reducing the need for unnecessary iterations on the FE.
Summary
The OCX 2024 AGM was an opportunity for the OCX family to meet and exchange experiences, discuss use cases and unite in promoting the OCX as a catalyst for change. We all share the same vision and see the OCX as an enabler for digitalisation for the shipbuilding industry. It was also interesting to see that the event attracted participants representing shipowners (Venture Ship Management) and manufacturers (NMC Technical Insulations) indicating that the OCX is starting to attract other stakeholders than designers/yards and classification societies. Let us make the OCX family greater together!
A big thanks to all of you for having made the event a great success.
OCX Chair
Ole Christian Astrup Ph.D
3D Approval Transformation
Ship Classification
Maritime
DNV AS
dnv.com|LinkedIn